Conditioning
Plant Process
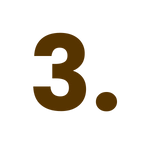
Conditioning
Your tobacco deserves the best treatment possible. Therefore GTC developed individual conditioning processes for lamina and stems.
Direct Conditioning Cylinder (DCC)
LOOSENING AND ENRICHING OF TOBACCO
The GTC DCC is designed for providing the best achievement in direct conditioning and opening of all types of Leaf Tobacco.
Before the process, a heat exchanger is used to pre-heat the drum.
A process air loop system conditioned by spray steam guarantees the best environment for warming up and loosening the tobacco leaves.
Process water added by two-substance nozzles ensures the required moisture of the tobacco.
The lamina slices will be gently opened by a pins and paddles combination of the rotating cylinder in the conditioned environment.
Direct-driven support rollers ensure a low noise level.
The discharge hood is designed with rounded edges and equipped with water spray nozzles which allow effective cleaning after the process.
A service cubicle with all necessary instruments for the conditioning process is positioned next to the conditioning cylinder.
Direct Conditioning Cylinder Casing (DCC-C)
Additionally, our basic DCC can be extended for a complete process of conditioning and casing tobacco. The GTC DCC-C is equipped with a complete application for spraying casing on tobacco, with a dual nozzle for casing and steam in the outlet hood. The metering systems for casing and steam are integrated into the extended fittings cabinet. The supply lines for sauce and steam are thermally insulated.
TWISTER (DCP-C)
THE NEW WAY OF CONDITIONING
The Twister is a compact process unit developed by GTC for the treatment of various tobacco products in the PMD.
DCP-C = Conditioning of stems and cloves
The high efficiency is realized by the rotation of two specially designed star wheels which allows no build-ups or product accumulation inside the Twister.
Due to this design, the TWISTER can process even long fibre products without roping.
A special steam injection ensures a perfect product penetration in combination with water injection by two substance nozzles which leads to the highest conditioning results in a matter of 15-20 seconds.
The Twister stands for low energy consumption, small footprint and especially for best practice in service and maintenance.
The TWISTER is easy to integrate into existing product lines.
DCP-S = Conditioning of Cut Rag and Cigar Filler
Additional process variations of the TWISTER are the conditioning of cut rag before the CO2 expansion and the flavor or PG application of cut rag or cigar filler. For these processes the steam injection can be replaced by compressed air in order for a gentle and cold product treatment.